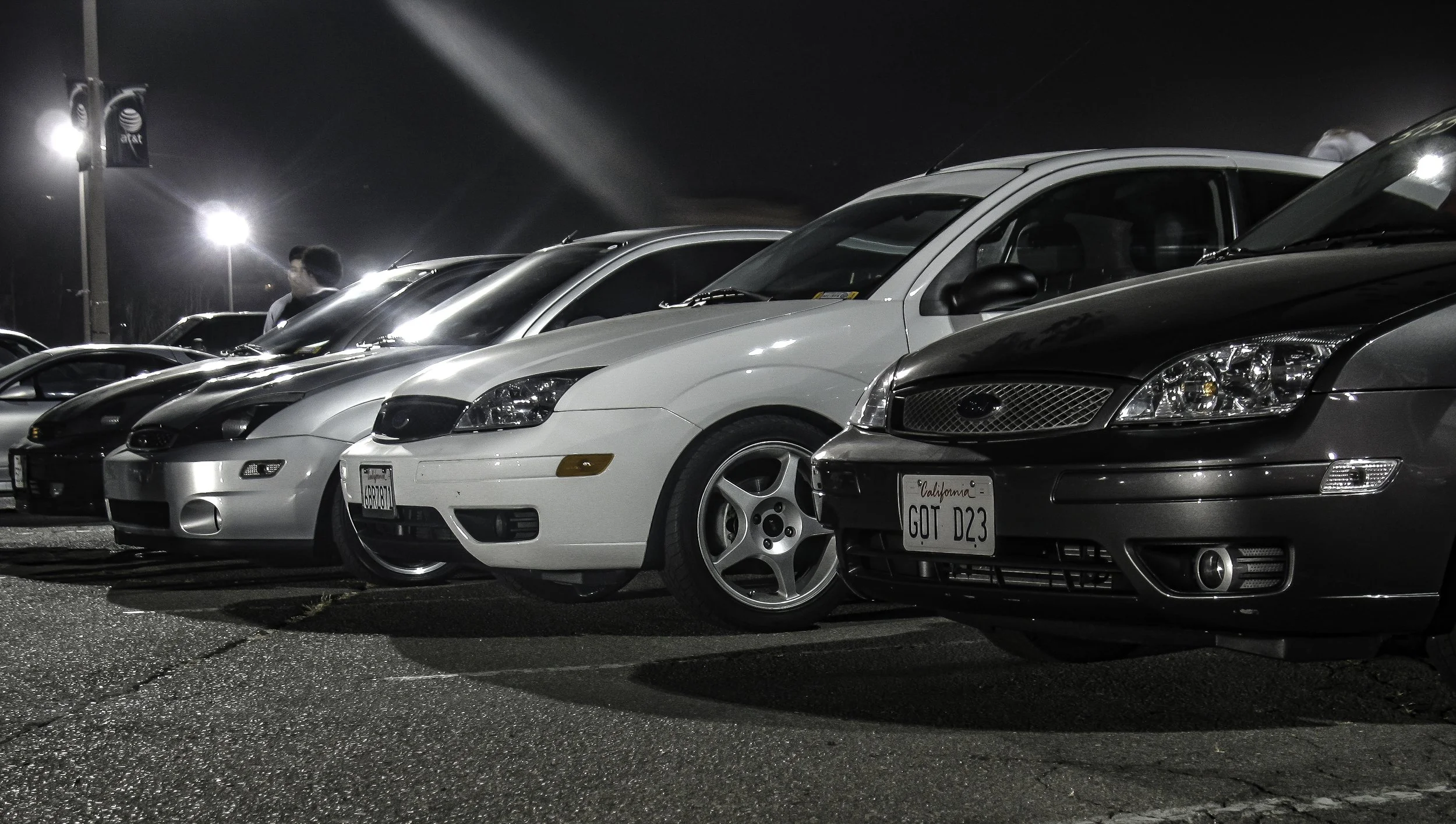
DTC Codes For MK1 Focus (2000-2007)
DTC, or Diagnostic Trouble Codes, are generated by the car’s on-board diagnostic (OBDII) system when a fault in the system is detected. when a dtc is present, the malfunction indicator lamp (MIL) also known as the Check Engine Light (CEL), will illuminate. you can then use a handheld code scanner to plug into the obdii port located under the drivers side dash to read the codes.
***** These codes are provided for reference only. FocusRush.com does not accept any responsibility for any damages to your vehicle that may result in the misuse of this information. Always consult a professional before working on your vehicle.
-
P0102- Mass Air Flow (MAF) Circuit Low Input
The MAF sensor circuit is monitored by the PCM for low air flow (measured in voltage) through the comprehensive component monitor (CCM). If during KEY ON and engine running, the air flow (or voltage) changes below a minimum calibrated limit, the test fails.Possible Causes
MAF sensor disconnected
MAF circuit open to PCM
VPWR open to MAF sensor
PWR GND open to MAF sensor
MAF RTN circuit open to PC
MAF circuit shorted to GND
Intake air leak (near MAF sensor)
A closed throttle indication [throttle position (TP) sensor system]
Damaged or dirty MAF sensor
Damaged PCM
Possible Solutions
It is very common for the wiring insulation to degrade on the MAF pigtail. Inspect the wiring insulation where the wires go inside the plastic connector housing for signs of damage. If damaged, wire in a new pigtail following proper soldering techniques and use waterproof connections.
Remove and inspect the MAF Sensor itself. If the sensor appears damaged, replace with a new MAF sensor. If the sensor is dirty, you can attempt to clean it using a cleaning solution designed for mass airflow sensors. If cleaning does not work, replace with a new MAF sensor.oes here
-
The MAF sensor circuit is monitored by the PCM for low air flow (measured in voltage) through the comprehensive component monitor (CCM). If during KEY ON and engine running, the air flow (or voltage) changes below a maximum calibrated limit, the test fails.
Possible Causes
MAF sensor screen is blocked
MAF circuit shorted to VPWR
Damaged or dirty MAF sensor
Damaged PCM
Possible Solutions
It is very common for the wiring insulation to degrade on the MAF pigtail. Inspect the wiring insulation where the wires go inside the plastic connector housing for signs of damage. If damaged, wire in a new pigtail following proper soldering techniques and use waterproof connections.
Remove and inspect the MAF Sensor itself. If the sensor appears damaged, replace with a new MAF sensor. If the sensor is dirty, you can attempt to clean it using a cleaning solution designed for mass airflow sensors. If cleaning does not work, replace with a new MAF sensor.ription text goes here
-
The MAF sensor circuit is monitored by the PCM for low air flow (measured in voltage) through the comprehensive component monitor (CCM). If during KEY ON and engine running, the air flow (or voltage) changes below a maximum calibrated limit, the test fails.
Possible Causes
MAF sensor screen is blocked
MAF circuit shorted to VPWR
Damaged or dirty MAF sensor
Damaged PCM
Possible Solutions
It is very common for the wiring insulation to degrade on the MAF pigtail. Inspect the wiring insulation where the wires go inside the plastic connector housing for signs of damage. If damaged, wire in a new pigtail following proper soldering techniques and use waterproof connections.
Remove and inspect the MAF Sensor itself. If the sensor appears damaged, replace with a new MAF sensor. If the sensor is dirty, you can attempt to clean it using a cleaning solution designed for mass airflow sensors. If cleaning does not work, replace with a new MAF sensor.
-
BARO/MAF sensor operating voltage is less than 0.25 volts (VREF), as a result it failed below the minimum calibrated parameter.
Possible Causes
Open circuit or short to ground
VREF circuit open or short to ground
Damaged or dirty BARO/MAF sensor
Possible Solutions
It is very common for the wiring insulation to degrade on the BARO/MAF pigtail. Inspect the wiring insulation where the wires go inside the plastic connector housing for signs of damage. If damaged, wire in a new pigtail following proper soldering techniques and use waterproof connections.
Remove and inspect the BARO/MAF Sensor itself. If the sensor appears damaged, replace with a new BARO/MAF sensor. If the sensor is dirty, you can attempt to clean it using a cleaning solution designed for mass airflow sensors. If cleaning does not work, replace with a new BARO/MAF sensor.
-
BARO/MAF operating voltage is greater than 5.0 volts (VREF), as a result it failed above maximum allowable calibrated parameter.
Possible Causes
VREF shorted to VWPR
BARO/MAF signal shorted to VPWR
Damaged or dirty BARO/MAP sensor
Damaged PCM
Possible Solutions
It is very common for the wiring insulation to degrade on the BARO/MAF pigtail. Inspect the wiring insulation where the wires go inside the plastic connector housing for signs of damage. If damaged, wire in a new pigtail following proper soldering techniques and use waterproof connections.
Remove and inspect the BARO/MAF Sensor itself. If the sensor appears damaged, replace with a new BARO/MAF sensor. If the sensor is dirty, you can attempt to clean it using a cleaning solution designed for mass airflow sensors. If cleaning does not work, replace with a new BARO/MAF sensor.
-
The sensor signal to the PCM is failing intermittently
Possible Causes
Loose electrical connection
Damaged or dirty BARO/MAF sensor
Possible Solutions
Check the connector going to the BARO/MAF sensor to verify it is seated properly. Unplug the connector and plug it back in, insuring you hear the locking mechanism click together.
It is very common for the wiring insulation to degrade on the BARO/MAF pigtail. Inspect the wiring insulation where the wires go inside the plastic connector housing for signs of damage. If damaged, wire in a new pigtail following proper soldering techniques and use waterproof connections.
Remove and inspect the BARO/MAF Sensor itself. If the sensor appears damaged, replace with a new BARO/MAF sensor. If the sensor is dirty, you can attempt to clean it using a cleaning solution designed for mass airflow sensors. If cleaning does not work, replace with a new BARO/MAF sensor.
-
Intake Air Temperature (IAT) sensor indicates the sensor signal is less than the Self-Test Minimum. The IAT sensor minimum is 0.2 volts. IAT V PID reading less than 0.2 volts with key ON and engine OFF or during any engine operating mode indicates a hard fault. The Intake Air Temperature Sensor is integrated into the Mass Air Flow (MAF) sensor and cannot be replaced separately.
Possible Causes
Loose electrical connection
Grounded circuit in harness
Damaged or dirty IAT sensor
Possible Solutions
Check the connector going to the IAT/MAF sensor to verify it is seated properly. Unplug the connector and plug it back in, insuring you hear the locking mechanism click together.
It is very common for the wiring insulation to degrade on the IAT/MAF pigtail. Inspect the wiring insulation where the wires go inside the plastic connector housing for signs of damage. If damaged, wire in a new pigtail following proper soldering techniques and use waterproof connections.
Remove and inspect the IAT/MAF Sensor itself. If the sensor appears damaged, replace with a new IAT/MAF sensor. If the sensor is dirty, you can attempt to clean it using a cleaning solution designed for mass airflow sensors. If cleaning does not work, replace with a new IAT/MAF sensor.
-
Indicates the sensor signal is greater than the Self-Test Maximum. IAT V PID reading greater than 4.6 volts with key ON and engine OFF or during any engine operating mode indicates a hard fault. The Intake Air Temperature Sensor is integrated into the Mass Air Flow (MAF) sensor and cannot be replaced separately.
Possible Causes
Loose electrical connection
Open circuit in harness
Sensor signal short to power
Damaged or dirty IAT sensor
Damaged PCM
Possible Solutions
Check the connector going to the IAT/MAF sensor to verify it is seated properly. Unplug the connector and plug it back in, insuring you hear the locking mechanism click together.
It is very common for the wiring insulation to degrade on the IAT/MAF pigtail. Inspect the wiring insulation where the wires go inside the plastic connector housing for signs of damage. If damaged, wire in a new pigtail following proper soldering techniques and use waterproof connections.
Remove and inspect the IAT/MAF Sensor itself. If the sensor appears damaged, replace with a new IAT/MAF sensor. If the sensor is dirty, you can attempt to clean it using a cleaning solution designed for mass airflow sensors. If cleaning does not work, replace with a new IAT/MAF sensor.
-
Indicates the engine coolant temperature rationality test has failed. The PCM logic that sets this DTC indicates that engine coolant temperature sensor (ECT or CHT) drifted higher than the nominal sensor calibration curve and could prevent one or more OBD II monitors from executing. The PCM runs this logic after an engine off “calibrated soak period (typically 6 hours). This soak period allows the Intake Air Temperature (IAT) and engine coolant temperature (CHT or ECT) to stabilize and not differ by more than a calibrated value. A failure of this sensor can cause the car to go into LIMP mode, a fail-safe mode which can cause significantly reduced power and speed, and cause things like the air conditioner to stop working.
Possible Causes
Low engine coolant level
Faulty Engine Coolant Temperature (ECT) sensor
Faulty engine coolant thermostat
Engine Coolant Temperature (ECT) sensor harness is open or shorted
Engine Coolant Temperature (ECT) sensor circuit poor electrical connection
Possible Solutions
Inspect the the coolant level while the engine has had a chance to cool down to verify the coolant level is between the MIN/MAX lines. If the coolant level on a cold engine is low, slowly open the degas tank cap and fill with coolant until it is between the MIN/MAX lines. DO NOT DO THIS WHILE THE ENGINE IS STILL HOT. THE COOLANT SYSTEM IS UNDER PRESSURE. REMOVING THE CAP WHILE THE ENGINE IS STILL HOT CAN CAUSE THE COOLANT TO RUSH OUT OF THE DEGAS TANK, CAUSING SEVERE BURNS.
Check the connector going to the ECT sensor to verify it is seated properly. Unplug the connector and plug it back in, insuring you hear the locking mechanism click together.
Inspect the wiring leading to the ECT sensor for damage. If damaged, repair the wiring using waterproof connections.
Replace the ECT sensor
-
Indicates the sensor signal is less than Self-Test minimum. The ECT sensor minimum is 0.2 volts or 121°C (250°F). Note on some vehicles that are not equipped with an ECT sensor, CHT can be used and can set this DTC
Possible Causes
Loose electrical connection
Grounded circuit in the harness
Damaged sensor
Damaged PCM
Possible Solutions
Check the connector going to the ECT sensor to verify it is seated properly. Unplug the connector and plug it back in, insuring you hear the locking mechanism click together.
Inspect the wiring leading to the ECT sensor for damage. If damaged, repair the wiring using waterproof connections.
Replace the ECT sensor
-
Indicates the sensor signal is greater than Self-Test maximum. The ECT sensor maximum is 4.6 volts or -50°C (-58°F). Note on some vehicles that are not equipped with an ECT sensor, CHT can be used and can set this DTC.
Possible Causes
Loose electrical connection
Open circuit in the harness
Sensor signal short to power
Damaged sensor
Damaged PCM
Possible Solutions
Check the connector going to the ECT sensor to verify it is seated properly. Unplug the connector and plug it back in, insuring you hear the locking mechanism click together.
Inspect the wiring leading to the ECT sensor for damage. If damaged, repair the wiring using waterproof connections.
Replace the ECT sensor
-
The Throttle Position (TP) sensor circuit is monitored by the PCM for a non-closed throttle position at idle. If KEY ON engine running self-test terminates upon placing the transmission range selector in gear (DRIVE or REVERSE) or when closing the throttle (idle) after opening it (in PARK or NEUTRAL), the TP closed throttle position is not attained, the test fails.
Possible Causes
Binding throttle cable at the throttle body
TP circuit short to PCM
Damaged TP Sensor
Damaged, warped, or dirty throttle body
SIG RTN circuit open to TP sensor
Possible Solutions
Check the throttle cable to verify that it is not getting caught on other wires inside the engine bay, causing the throttle plate to stick open.
Remove the intake boot and inspect the throttle body for damage or dirt buildup
With the ENGINE OFF, move the throttle plate back and forth to see if the plate is sticking. If so, remove the throttle body and clean with a cleaning solution designed for throttle bodies.
Inspect the wiring near the TP sensor for damage. If damaged, repair the wiring using waterproof connections.
Replace the TP sensor
-
The Throttle Position (TP) sensor circuit is monitored by the PCM for a low TP rotation angle (or voltage) input through the Comprehensive Component Monitor (CCM). If during KEY ON and ENGINE OFF, or KEY ON and ENGINE RUNNING, the TP rotation angle (or voltage) changes below a minimum calibrated limit, the test fails.
Possible Causes
TP sensor is not seated properly
TP circuit open to PCM
TP circuit short to GND
VREF open to TP sensor
Damaged TP Sensor
Damaged PCM
Possible Solutions
Check the plastic connector to verify that it is seated properly. Unplug the connector and plug it back in, making sure to listen for the interlocking mechanism to click into place.
Inspect the wiring near the TP sensor for damage. If damaged, repair the wiring using waterproof connections.
Replace the TP sensor.
-
The Throttle Position (TP) sensor circuit is monitored by the PCM for a high TP rotation angle (or voltage) input through the Comprehensive Component Monitor (CCM). If during KEY ON and ENGINE OFF, or KEY ON and ENGINE RUNNING, the TP rotation angle (or voltage) changes above the maximum calibrated limit, the test fails.
Possible Causes
TP sensor not seated properly
TP circuit short to PWR
VREF short to PWR
SIG RTN circuit open to TP sensor
Damaged TP sensor
Damaged PCM
Possible Solutions
Check the plastic connector to verify that it is seated properly. Unplug the connector and plug it back in, making sure to listen for the interlocking mechanism to click into place.
Inspect the wiring near the TP sensor for damage. If damaged, repair the wiring using waterproof connections.
Replace the TP sensor.
-
Indicated the Engine Coolant Temperature (ECT) or Cylinder Head Temperature (CHT) sensor has not achieved the required temperature level to enter closed loop operating conditions within a specified amount of time after the engine has been started.
Possible Causes
Insufficient warm up time
Low engine coolant level
Leaking or stuck thermostat
Malfunctioning ECT sensor
Malfunctioning CHT sensor
Possible Solutions
Inspect the the coolant level while the engine has had a chance to cool down to verify the coolant level is between the MIN/MAX lines. If the coolant level on a cold engine is low, slowly open the degas tank cap and fill with coolant until it is between the MIN/MAX lines. DO NOT DO THIS WHILE THE ENGINE IS STILL HOT. THE COOLANT SYSTEM IS UNDER PRESSURE. REMOVING THE CAP WHILE THE ENGINE IS STILL HOT CAN CAUSE THE COOLANT TO RUSH OUT OF THE DEGAS TANK, CAUSING SEVERE BURNS.
Inspect the thermostat housing for signs of leaking. If you have been experiencing problems with the HVAC system blowing hot air through the cabin vents, it’s likely the thermostat is bad and needs to be replaced.
Inspect the coolant lines for signs of leaking. If a leak is found, replace the damaged coolant line.
Replace the Engine Coolant Temperature (ECT) sensor.
Replace the Cylinder Head Temperature (CHT) sensor.
-
Indicates that the Intake Air Temperature (IAT) sensor has detected a potential abnormality in the air intake system. The sensor uses a thermistor which is sensitive in changes to temperature. The electrical resistance decreases when the temperatures rise. The Intake Air Temperature Sensor is integrated into the Mass Air Flow (MAF) sensor and cannot be replaced separately.
Possible Causes
Dirty air filter
Loose electrical connection
Damaged wiring harness to the Mass Air Flow (MAF) sensor
Damaged or dirty Mass Air Flow (MAF) sensor
Damaged PCM
Possible Solutions
Remove the airbox and inspect the inside for debris, and remove debris if any found.
Inspect the air filter for contamination, and replace if needed.
Check the plastic connector on the MAF to verify that it is seated properly. Unplug the connector and plug it back in, making sure to listen for the interlocking mechanism to click into place.
It is very common for the wiring insulation to degrade on the MAF pigtail. Inspect the wiring insulation where the wires go inside the plastic connector housing for signs of damage. If damaged, wire in a new pigtail following proper soldering techniques and use waterproof connections.
Remove and inspect the MAF Sensor itself. If the sensor appears damaged, replace with a new MAF sensor. If the sensor is dirty, you can attempt to clean it using a cleaning solution designed for mass airflow sensors. If cleaning does not work, replace with a new MAF sensor.
-
The Heated Oxygen Sensor (HO2S) is monitored for a negative voltage known as a Characteristic Shift Downward (CSD). If the sensor is thought to be switching from 0 volts to -1 volts during testing, the PCM will use this input and remain in fuel control.
Possible Causes
Contaminated HO2S sensor (water, fuel, etc.)
Crossed HO2S signal/return wiring
Possible Solutions
Check the plastic connector on the HO2S to verify that it is seated properly. Unplug the connector and plug it back in, making sure to listen for the interlocking mechanism to click into place.
Inspect the wiring near the HO2S sensor for damage. If damaged, repair the wiring using waterproof connections.
Replace the HO2S sensor.
-
The Heated Exhaust Gas (HEGO) Monitor checked the Heated Oxygen Sensor (HO2S) frequency and amplitude. If during testing the frequency and amplitude were to fall below a calibrated limit, the test will fail.
Possible Causes
Contaminated HO2S sensor (water, fuel, etc.)
Deteriorating HO2S sensor
Exhaust leak
Shorted or open wiring
Improper fueling
Damaged Mass Air Flow (MAF) sensor
Intake air leaks
Possible Solutions
Check the plastic connector on the HO2S to verify that it is seated properly. Unplug the connector and plug it back in, making sure to listen for the interlocking mechanism to click into place.
Inspect the wiring near the HO2S sensor for damage. If damaged, repair the wiring using waterproof connections.
Inspect the exhaust system for holes
Replace the HO2S sensor
Check the plastic connector on the MAF to verify that it is seated properly. Unplug the connector and plug it back in, making sure to listen for the interlocking mechanism to click into place.
It is very common for the wiring insulation to degrade on the MAF pigtail. Inspect the wiring insulation where the wires go inside the plastic connector housing for signs of damage. If damaged, wire in a new pigtail following proper soldering techniques and use waterproof connections.
Remove and inspect the MAF Sensor itself. If the sensor appears damaged, replace with a new MAF sensor. If the sensor is dirty, you can attempt to clean it using a cleaning solution designed for mass airflow sensors. If cleaning does not work, replace with a new MAF sensor.
Inspect the air intake system for leaks
-
During testing, the Heated Oxygen Sensor (HO2S) heaters are checked for opens/shorts and excessive current draw. The test fails when current draw exceeds a calibrated limited and/or an open short is detected.
Possible Causes
Short to VPWR in harness or HO2S
Water in harness connector
Open VPWR circuit
Open GND circuit
Corrosion or poor mating terminals and wiring
Damaged HO2S sensor
Low battery voltage
Damaged PCM
Possible Solutions
Inspect the wiring near the HO2S sensor for damage. If damaged, repair the wiring using waterproof connections.
Check the plastic connector on the HO2S to verify that it is seated properly. Unplug the connector and plug it back in, making sure to listen for the interlocking mechanism to click into place.
Inspect the HO2S connector to see if the water seal is damaged, and water pooled inside the connector. If so, replace the wiring to the HO2S following proper soldering techniques and use waterproof connections.
Replace the HO2S sensor
-
The downstream HO2S sensor is continuously checked for maximum and minimum voltages. The test fails when the voltages fail to meet the calibrated limits.
Possible Causes
Pinched, shorted, or corroded wiring and pins
Crossed sensor wires
Exhaust leaks
Contaminated HO2S sensor (water, fuel, etc.)
Deteriorating HO2S sensor
Possible Solutions
Inspect the wiring near the HO2S sensor for damage. If damaged, repair the wiring using waterproof connections.
Check the plastic connector on the HO2S to verify that it is seated properly. Unplug the connector and plug it back in, making sure to listen for the interlocking mechanism to click into place.
Inspect the exhaust system for holes
Replace the HO2S sensor
-
DOWNSTREAM SENSOR POST-CATALYTIC CONVERTER. SEE DTC P0135 FOR MORE INFORMATION
-
The Fuel Injection Control Module (FICMM) has detected a deviation between the pre-calibrated set point and the actual fuel pressure, causing one bank to be lean at wide open throttle.
Possible Causes
Severely restricted fuel filter
Severely restricted fuel supply line
Damaged or faulty fuel pump
Damaged or dirty Mass Air Flow (MAF) sensor
Possible Solutions
Remove and replace the fuel filter, located at the back of the car near the fuel tank.
After the car has been off for 15-20 minutes, turn the key to the KEY ON position and listen for the fuel pump to prime.
-
The Adaptive Fuel Strategy continuously monitors fuel delivery. This code indicates there is too much air and not enough fuel. Presence of this DTC can make the car run abnormally, may cause coolant temps to rise due to hotter combustion cycle, or be down on power.
Possible Causes
Intake air leaks after the Mass Air Flow (MAF) sensor
Deteriorating Heated Oxygen Sensor (HO2S)
Exhaust leaks before the Heated Oxygen Sensor (HO2S)
Vacuum leaks
Clogged or non-functioning fuel injectors
Incorrect fuel pressure
Faulty or leaking fuel pressure regulator
Running low on fuel
Fault in the vapor recovery system
Defective Positive Crankcase Ventilation (PCV) system
Stuck Exhaust Gas Recirculation (EGR) valve
Incorrect cam timing
Low cylinder compression
Oil overfilled
Possible Solutions
Inspect for air leaks after the Mass Air Flow (MAF) sensor. Common spots for leaks to occur are at the boot going from the intake to the throttle body, faulty throttle body gaskets, and faulty intake manifold gaskets.
Inspect the wiring near the Heated Oxygen (HO2S) sensor for damage. If damaged, repair the wiring using waterproof connections.
Replace the Heated Oxygen Sensor (HO2S).
Inspect the vacuum lines for loose or damaged hoses. Vacuum routing diagram can be found on the underside of the hood.
Inspect the vapor canister on the firewall of the passenger side of the engine bay for cracks and corroded lines.
Inspect the Positive Crankcase Ventilation (PCV) system for damage or collapsed rubber hoses.
Replace the Positive Crankcase Ventilation (PCV) valve
Inspect the Exhaust Gas Recirculation (EGR) valve for damage
If the timing belt has recently been changed, verify the timing has not moved.
Check for cylinder compression using a compression tool.
Use the oil dipstick to verify that the oil has not been overfilled.
-
The Adaptive Fuel Strategy continuously monitors the fuel delivery hardware. This test will fail when there’s too much fuel and not enough air.
Possible Causes
Excessive fuel pressure due to a restriction in the fuel line
Faulty fuel pressure regulator
Leaking fuel injector
Air intake system restriction
Clogged exhaust system (catalytic converter, exhaust pipe, or muffler)
Exhaust leak upstream of the Heated Oxygen Sensor (HO2S)
Loose electrical connections at the Mass Air Flow (MAF) sensor
Possible Solutions
This code will also show up with other fueling related problems (P0148).
Inspect the wiring leading to the fuel pressure regulator for damage. If damaged, repair the wiring using waterproof connections.
Remove and inspect the fuel injectors, paying close attention to the rubber O-Rings. If the O-Rings are damaged, replace them. If the injector is saturated in fuel, this is a likely culprit, replace the fuel injector.
Remove the airbox cover lid and inspect the air intake system for debris. Inspect the filter and replace if contaminated.
Inspect the exhaust for holes or loose fittings above the HO2S sensors.
Check the plastic connector on the MAF to verify that it is seated properly. Unplug the connector and plug it back in, making sure to listen for the interlocking mechanism to click into place.
It is very common for the wiring insulation to degrade on the MAF pigtail. Inspect the wiring insulation where the wires go inside the plastic connector housing for signs of damage. If damaged, wire in a new pigtail following proper soldering techniques and use waterproof connections.
Remove and inspect the MAF Sensor itself. If the sensor appears damaged, replace with a new MAF sensor. If the sensor is dirty, you can attempt to clean it using a cleaning solution designed for mass airflow sensors. If cleaning does not work, replace with a new MAF sensor.
-
The Comprehensive Component Monitor (CCM) monitors the Engine Fuel Temperature (EFT) sensor circuit to the PCM for low and high voltage. If voltage were to fall below or exceed a calibrated limit and amount of time during testing, the test will fail. The EFT sensor is a part of the Fuel Rail Pressure Sensor, and cannot be replaced separately.
Possible Causes
Open or short in the harness
Faulty Fuel Rail Pressure Sensor
Loose electrical connection
Low ambient temperature operation
Damaged PCM
Possible Solutions
Inspect the wiring harness leading to the Fuel Rail Pressure Sensor for signs of damage or cracked insulation on the wiring. If damaged, repair the wiring using waterproof connections.
Check the plastic connector on the Fuel Rail Pressure Sensor to verify that it is seated properly. Unplug the connector and plug it back in, making sure to listen for the interlocking mechanism to click into place.
Replace the Fuel Rail Pressure Sensor
-
The Comprehensive Component Monitor (CCM) monitors the Engine Fuel Temperature (EFT) for acceptable operating temperature. If during testing the voltage were to fall below or exceed a calibrated limit during a calibrated amount of time, the test will fail.
SEE DTC P0180 FOR MORE INFORMATION
-
The Comprehensive Component Monitor (CCM) monitors the Engine Fuel Temperature (EFT) sensor circuit to the PCM for low voltage. If voltage were to fall below a calibrated limit and amount of time during testing, the test will fail.
SEE DTC P0180 FOR MORE INFORMATION
-
The Comprehensive Component Monitor (CCM) monitors the Engine Fuel Temperature (EFT) sensor circuit to the PCM for high voltage. If the voltage were to exceed above a calibrated limit and amount of time during testing, the test will fail.
SEE DTC P0180 FOR MORE INFORMATION
-
The Comprehensive Component Monitor (CCM) monitors the Fuel Rail Pressure Sensor (FPR) to the PCM for VREF voltage. The test fails when the VREF voltage from the PCM drops to a voltage less than the minimum calibrated value.
Possible Causes
VREF open in harness
VREF open in sensor
VREF open in PCM
Possible Solutions
Inspect the wiring harness leading to the Fuel Rail Pressure Sensor for signs of damage or cracked insulation on the wiring. If damaged, repair the wiring using waterproof connections.
Check the plastic connector on the Fuel Rail Pressure Sensor to verify that it is seated properly. Unplug the connector and plug it back in, making sure to listen for the interlocking mechanism to click into place.
-
he Comprehensive Component Monitor (CCM) monitors the Fuel Rail Pressure Sensor (FRP) pressure for acceptable fuel pressure. The test fails when the fuel pressure falls below or exceeds a minimum/maximum calibrated value for a calibrated period of time.
Possible Causes
High Fuel Pressure (See DTC P0170/P0171)
Low Fuel Pressure (See DTC P0170/P0171)
Damaged FRP sensor
Excessive resistance in circuit
Low or no fuel
Possible Solutions
Inspect the wiring harness leading to the Fuel Rail Pressure Sensor for signs of damage or cracked insulation on the wiring. If damaged, repair the wiring using waterproof connections.
Check the plastic connector on the Fuel Rail Pressure Sensor to verify that it is seated properly. Unplug the connector and plug it back in, making sure to listen for the interlocking mechanism to click into place.
See details on DTC P0170 and P0171 for more troubleshooting steps.
Replace the FRP sensor
-
The Comprehensive Component Monitor (CCM) monitors the Fuel Rail Pressure Sensor (FRP) circuit to the PCM for low voltage. If the voltage were to fall below a calibrated limit and amount of time during testing, the test will fail.
Possible Causes
FRP signal shorted to SIG RTN or PWR GND
Damaged or faulty FRP Sensor
Damaged PCM
Possible Solutions
Inspect the wiring harness leading to the Fuel Rail Pressure Sensor for signs of damage or cracked insulation on the wiring. If damaged, repair the wiring using waterproof connections.
Check the plastic connector on the Fuel Rail Pressure Sensor to verify that it is seated properly. Unplug the connector and plug it back in, making sure to listen for the interlocking mechanism to click into place.
See details on DTC P0170 and P0171 for more troubleshooting steps.
Replace the FRP sensor
-
The Comprehensive Component Monitor (CCM) monitors the Fuel Rail Pressure Sensor (FRP) circuit to the PCM for high voltage. If the voltage were to exceed a calibrated limit and a calibrated amount of time during testing, the test will fail.
Possible Causes
FRP signal shorted to VREF or VPWR
FRP signal open
Damaged for faulty FRP sensor
Damaged PCM
Possible Solutions
Inspect the wiring harness leading to the Fuel Rail Pressure Sensor for signs of damage or cracked insulation on the wiring. If damaged, repair the wiring using waterproof connections.
Check the plastic connector on the Fuel Rail Pressure Sensor to verify that it is seated properly. Unplug the connector and plug it back in, making sure to listen for the interlocking mechanism to click into place.
See details on DTC P0170 and P0171 for more troubleshooting steps.
Replace the FRP sensor
-
The Comprehensive Component Module (CCM) monitors the operation of the fuel injector drivers in the PCM. The test fails when the fuel injector does not operate electrically, even though the harness assembly and fuel injectors pass self-testing.
Possible Causes
Faulty fuel injector on the corresponding cylinder
Damaged wiring harness to corresponding fuel injector
Faulty fuel injector driver in the PCM
Possible Solutions
Remove and inspect the fuel injector on the corresponding cylinder for damage.
Replace fuel injector
Inspect the wiring harness leading to the corresponding fuel injector for signs of damage or cracked insulation on the wiring. If damaged, repair the wiring using waterproof connections.
Check the plastic connector on the fuel injector to verify that it is seated properly. Unplug the connector and plug it back in, making sure to listen for the interlocking mechanism to click into place.
-
Indicates an engine overheat condition was detected by the Cylinder Head Temperature (CHT) sensor. This condition can cause significant engine damage if driven for prolonged periods of time without diagnosing the root cause.
Possible Causes
Low engine coolant level
Clogged radiator
Faulty radiator fan switch
Faulty radiator fan switch wiring
Stuck or leaking thermostat
Faulty CHT sensor
Possible Solutions
Inspect the the coolant level while the engine has had a chance to cool down to verify the coolant level is between the MIN/MAX lines. If the coolant level on a cold engine is low, slowly open the degas tank cap and fill with coolant until it is between the MIN/MAX lines. DO NOT DO THIS WHILE THE ENGINE IS STILL HOT. THE COOLANT SYSTEM IS UNDER PRESSURE. REMOVING THE CAP WHILE THE ENGINE IS STILL HOT CAN CAUSE THE COOLANT TO RUSH OUT OF THE DEGAS TANK, CAUSING SEVERE BURNS.
Inspect the coolant hoses going into and coming out of the radiator for signs of fluid. The hoses can be squeezed by hand, and you should be able to feel coolant flowing through the hoses when compressed.
Remove and inspect the radiator fan switch sensor and wiring for signs of corrosion or damage. If corrosion or damage is found in one or both of the units, replace the switch/harness.
Inspect the thermostat housing for signs of leaking. If you have been experiencing problems with the HVAC system blowing hot air through the cabin vents, it’s likely the thermostat is bad and needs to be replaced.
Inspect the coolant lines for signs of leaking. If a leak is found, replace the damaged coolant line.
Replace the CHT sensor
-
The PCM monitors the Fuel Pump (FP) circuit output from the PCM. The test fails if: with the FP output commanded ON (grounded); excessive current draw is detected on the FP circuit, or with the FP output commanded OFF, voltage is not detected on the FP circuit (the PCM expects to detect VPWR voltage coming through the fuel pump relay coil to the FP circuit).
Possible Causes
Damaged or faulty FP relay
Open or shorted FP circuit
Open VPWR circuit to the FP relay
Possible Solutions
Inspect the FP relay for damage (Power Distribution Box Location: R7)
Replace FP Relay (Power Distribution Box Location: R7)
Inspect the wiring harness leading to and from the fuel pump for signs of damage or cracked insulation on the wiring. If damaged, repair the wiring using waterproof connections
-
The PCM monitors the Fuel Pump Monitor (FPM) circuit. The test fails if the PCM commands the fuel pump ON and B+ voltage is not detected on the FPM circuit.
Possible Causes
Open B+ circuit to the fuel pump relay
Open FP PWR circuit between the fuel pump relay and it’s connection to the FPM circuit
Damaged FP Relay
Possible Solutions
Inspect the wiring harness leading to and from the fuel pump for signs of damage or cracked insulation on the wiring. If damaged, repair the wiring using waterproof connections.
Inspect the FP relay for damage (Power Distribution Box Location: R7)
Replace FP Relay (Power Distribution Box Location: R7)
-
The PCM monitors the Fuel Pump Monitor (FPM) circuit. This test fails when the PCM detects voltage on the FPM circuit while the fuel pump is commanded OFF. The FPM circuit is wired to a pull-up voltage inside the PCM. The FPM circuit will go high if, with the KEY ON and the fuel pump commanded OFF, the FPM/FP PWR circuit looses it’s path to the ground through the fuel pump. The FPM circuit will also go high if the FPM/FP PWR circuit is shorted to PWR.
Possible Causes
Inertia Fuel Shutoff (IFS) switch not reset or electrically open
Poor FP ground
FP electrically open
FP secondary circuits short to power
FP relay contacts always closed
Open FPM circuit between the PCM and connection to FP PWR circuit
Damaged Low Speed FP relay or concern with related circuits
Damaged PCM
Possible Solutions
Verify the Inertia Fuel Shutoff (IFS) switch has not been tripped. The button is located in the passenger footwell, head of the door.
Inspect the grounds off the fuel pump for corrosion. If corrosion exists, clean grounding surface and reattach ground.
-
Indicates the engine oil temperature protection strategy in the PCM has been activated. This will temporarily prohibit high engine speed operation by diabling injectors, therefore reducing the risk of engine damage from high engine oil temperature. On engines equipped with an oil temperature sensor, the PCM reads oil temperature to determine if it is excessive. When an oil temperature sensor is not present, the PCM uses an oil algorithm to infer actual temperature. Engine shutdown strategy function is the same on vehicles, regardless if it’s equipped with a sensor.
Possible Causes
Very high engine RPM for extended periods of time
Overheating condition
Possible Solutions
Your engine may be operating at high RPM’s due to an improper gear selection. Verify that the transmission is in Drive (Automatic Only), or you stay below 5000RPM consistently in a manual transmission.
See P0217 for Overheating information
-
The Random Misfire DTC indicates one or multiple cylinders are misfiring or the PCM cannot identify which cylinder is misfiring.
Possible Causes
Damaged, defective, or dirty spark plug(s)
Incorrect spark plug gap
Leaking valve cover gasket
Damaged or defective coil pack(s)
Damaged or defective spark plug wire
Damaged wiring leading to the coil pack(s)
Stuck or leaking fuel injector(s)
Faulty Camshaft Position Sensor (CMP)
Stuck open Exhaust Gas Recirculation (EGR) valve
Poor quality fuel
Incorrect camshaft timing
Low cylinder compression
Possible Solutions
Remove and inspect the spark plugs for signs fo damaged (cracked porcelin, missing or corroded ignitors, missing or corroded ground straps). If the plugs appear dirty or damaged, replace with new spark plugs.
Old spark plugs tend to gap themselves. Use a spark plug gap tool to verify the spark plug gap is still within preconfigured specifications.
It is extremely common for the valve cover gaskets to fail, causing the spark plug wells to fill with oil, reducing the effectiveness of the plug wires / coil on plug packs. Remove the spark plug wires or coil on plug packs to inspect for oil contamination. Replace valve cover gasket if necessary.
It is extremely common for the coil pack / coil on plug packs to go bad, sometimes without any visual indication that they are defective. Replace the coil pack / coil on plug pack.
It is extremely common for the spark plug wires to go bad, sometimes without any visual indication. Replace the spark plug wires.
It is extremely common on Zetec-based engines for the wires leading to the Coil Pack to have decayed insulation. Inspect the wiring leading into the plastic connector to the coil pack for signs of cracked or broken insulation. Replace the pigtail, if necessary, following proper soldering techniques and using waterproof connectors.
A fuel injector that is clogged, or one that is stuck open, can cause the cylinder to get improper fueling, resulting in a misfire.
Inspect the camshaft position sensor wiring for signs of damage. Repair the wiring leading to the camshaft position sensor, if necessary, following proper soldering techniques and using waterproof connectors.
Remove and inspect the Exhaust Gas Recirculation (EGR) valve for signs of damage. Replace if necessary.
Poor quality fuel can lead to random misfires. Other signs and symptoms include poor fuel economy and pinging/knocking.
If the timing belt has recently been replaced and the camshafts were not timed properly, you may see a random misfire code. This is typically accompanied by codes P1381 or P1383.
Low cylinder compression can also cause a random misfire code. Use a compression tester tool to verify the cylinders still have proper compression.
-
This DTC indicates that a misfire has been detected on a specific cylinder, the last number of the code designating which cylinder is the one that is misfiring. When this code appears, you will see the Check Engine Light (CEL) blink on and off repeatedly. Extended driving while this code is present can cause engine damage.
Please see P0300 for more information.
-
The Ignition Engine Speed Sensor input signal to the PCM is continually monitored. The test fails when the signal indicates that two successive erratic Profile Ignition Pickup (PIP) pulses have occurred.
Possible Causes
Arcing ignition components (coil, wires, plugs)
Interference with 2-way radios
Possible Solutions
Inspect the pigtail leading to the coil pack (SPI/Zetec Only). If the wires appear damaged, replace the pigtail leading to the ignition coil.
Inspect the ignition coil (SPI/Zetec) or Coil On Plug (Duratec) packs for signs of damage. If damaged, replace with new components.
Inspect the spark plug wires (SPI/Zetec) for signs of damage, replace if damage is found.
Remove and inspect the spark plugs for cracks in the porcelain on top. If damaged, replace with new spark plugs.
-
See DTC P0326
-
The Knock sensor detects vibrations upon increase and decrease in engine RPM. The knock sensor generates voltage based on this vibration. Should this voltage go outside a calibrated level, a DTC will set.
Possible Causes
Knock sensor wiring short to ground
Knock sensor circuit short to Power
Knock sensor circuit open
Damaged Knock Sensor
Damaged PCM
Possible Solutions
Inspect the wiring leading to the knock sensor for signs of damage. If damage is found, repair the wiring using proper soldering techniques and using waterproof connections.
Replace the Knock Sensor
-
The test fails when the PCM can no longer detect the signal from the Camshaft Position Sensor (CMP).
Possible Causes
CMP Circuit Short to ground
CMP circuit short to Power
Signal Return open (VR Sensor)
CMP Ground Open (Hall Effect Sensor)
Damaged CMP sensor shielding
Damaged CMP sensor
Harness routing, harness alterations, improper shielding, or electrical interference from other improperly functioning systems may also have intermittent impact on the CMP signal
Possible Solutions
Inspect the wiring leading to the CMP sensor, if damaged is found repair the wiring using proper soldering techniques and using waterproof connections.
Inspect the wiring near the CMP sensor, if damaged wiring is found, repair using proper soldering techniques and using waterproof connections.
Replace the CMP sensor.
-
The ignition circuit is continuously monitored. The test fails when the PCM does not receive a valid IDM pulse signal from the ignition module (integrated into the PCM).
Possible Causes
Open or short in Ignition START/RUN circuit
Open coil driver circuit
Coil Driver circuit shorted to ground
Damaged coil
Damaged PCM
Possible Solutions
Inspect the wiring leading to the main coil (SPI/Zetec) or coil packs (Duratec) for signs of damage. If damage is found, repair the wiring using proper soldering techniques and using waterproof connections.
Replace the coil (SPI/Zetec) or coil pack(s) (Duratec).
-
The Exhaust Gas Recirculation (EGR) system is monitored once per drive cycle during steady state conditions above 48 MPH. The test will fail when a malfunction is detected by PCM calculations indicating the EGR flow is less or greater than expected.
NOTE: ALL OF THE FOLLOWING SENSORS INPUT DATA TO THE PCM FOR PROPER OPERATION OF THE EGR SYSTEM: ENGINE COOLANT TEMPERATURE (ECT), CPS, INTAKE AIR TEMPERATURE (IAT), MASS AIR FLOW (MAF), THROTTLE POSITION (TP), MANIFOLD AIR PRESSURE (MAP). ANY DTC RELATED TO THE ABOVE MUST BE RESOLVED PRIOR TO TROUBLESHOOTING THIS CODE.
Possible Causes
EGR valve stuck open or closed
EGR connector not seated
EGR motor windings shorted or open circuit
No power to EGR
Harness open or shorted to Power or Ground
Vacuum signal to Mass Air Pressure (MAP) restricted or leaking
Mass Air Flow (MAF) sensor signal erroneous
Carbon buildup in EGR valve seat area
Damaged PCM
Possible Solutions
Remove and clean the area around the EGR valve
Verify the connector is seated properly
Replace the EGR valve
-
The Exhaust Gas Recirculation (EGR) system is monitored during steady state driving conditions while the EGR is commanded on. The test fails when the signal from the DPF EGR sensor indicates that the EGR flow is less than the desired minimum.
Possible Causes
Vacuum leak
EGR valve stuck closed
EGR valve leaks vacuum
EGR flow path restricted
EGR sensor short
Damaged EGR oriface tube
Damaged EGR solenoid
Damaged PCM
Possible Solutions
Check for vacuum leaks around the EGR sensor, inspect all vacuum lines for ill-fitting connections or damage in the vacuum lines.
Inspect the wiring going to the EGR sensor for damage. If damage is found, repair the wiring using proper soldering techniques and waterproof connections.
Replace the EGR
P0402 – EGR Flow Excessive Detected The EGR system is monitored for undesired EGR flow during idle. The EGR monitor looks at the DPF EGR signal
at idle
and compares it to the stored signal measured during key ON and engine OFF. The test fails when the signal at idle is greater than at key ON engine OFF
by a
calibrated amount. EGR valve stuck open
Plugged EGR vacuum regulator solenoid vent
Plugged EGR tube
Slow responding D.P.F. EGR sensor
Damaged DPF EGR sensor
Improper vacuum hose connection
Plugged vacuum hoses
EGRVR circuit shorted to ground
Damaged EGR vacuum regulator solenoid
Damaged PCM
A DPFEGR PID reading that is greater at idle than during key ON and engine OFF by 0.5 volt or a rough engine idle, may indicate a hard fault.
P0403 EEGR Electric Motor Windings Or Circuits To The PCM Shorted Or Open The EEGR system is continously monitored to check the 4 EEGR motor
coils,
circuits, and the PCM for opens, shorts to power and ground. If a malfunction is detected the EEGR system will be disabled and additional monitoring will
be
suspended for the remainder of the drive until the next drive cycle. EEGR motor windings open
Connector to EEGR not seated
Open circuit in harness from PCM to EEGR
Open circuit in PCM
Short circuit in EEGR motor
Short circuit in harness from PCM to EEGR
Short circuit in PCM
If an intermittent condition is suspected the most effective methoid of wiring fault isolation is to use the wiggle test methoid while measuring for shorts and
open
circuits.
P0411 – Secondary Air Injection (AIR) system upstream flow See DTC P1411
P0412 – Secondary Air Injection System (AIR) circuit malfunction The PCM attempts to control when air is injected in the exhaust. The DTC indicates a
Secondary Air injection system AIR circuit fault. AIR circuit open
AIR bypass solenoid fault
Damaged PCM
AIR circuit short to power
Solid state relay fault
Damaged AIR pump
The AIR circuit is normally held high through the AIR bypass solenoid and SSR when the output driver is off. Therefore, a low AIR circuit indicates a driver
is
always on and a high circuit indicates an open in the PCM.
P0420 – Catalyst System Efficiency Below Threshold (Bank 1) Indicates Bank 1 catalyst system efficiency is below the acceptable threshold Use of leaded
fuel
Damaged HO2S
Malfunctioning ECT
High fuel pressure
Damaged exhaust manifold
Damaged catalytic converter
Oil contamination
Cylinder misfiring
Downstream HO2S wires improperly connected
Damaged exhaust system pipe
Damaged muffler/tailpipe assembly
Retarded spark timing
Compare HO2S upstream and downstream switch rate and amplitude. Under normal closed loop fuel conditions, high efficiency catalysts have oxygen
storage
which makes the switching frequency of the downstream HO2S very slow and reduces the amplitude of those switches as compared to the upstream
HO2S. As
catalyst efficiency deteriorates, its ability to store oxygen declines and the downstream HO2S signal begins to switch more rapidly with increase amplitude,
approaching the switching rate and amplitude of the upstream HO2S. Once beyond an acceptable limit the DTC is set.
P0430 – Catalyst System Efficiency Below Threshold (Bank 2) Indicates Bank 2 catalyst system efficiency is below the acceptable threshold. Use of leaded
fuel
Damaged HO2S
Malfunctioning ECT
High fuel pressure
Damaged exhaust manifold
Damaged catalytic converter
Oil contamination
Cylinder misfiring
Downstream HO2S wires improperly connected
Damaged exhaust system pipe
Damaged muffler/tailpipe assembly
Retarded spark timing
Compare HO2S upstream and downstream switch rate and amplitude. Under normal closed loop fuel conditions, high efficiency catalysts have oxygen
storage
which makes the switching frequency of the downstream HO2S very slow and reduces the amplitude of those switches as compared to the upstream
HO2S. As
catalyst efficiency deteriorates, its ability to store oxygen declines and the downstream HO2S signal begins to switch more rapidly with increase amplitude,
approaching the switching rate and amplitude of the upstream HO2S. Once beyond an acceptable limit the DTC is set.
P0442 – EVAP Control System Leak Detected (Small Leak) The PCM monitors the complete EVAP control system for presence of a small fuel vapor leak.
The
system failure occurs when a fuel vapor leak from an opening as small as 1.016 mm (0.04 inch) is detected by the EVAP running loss monitor test.
After-market
EVAP hardware (such as fuel filler cap) non-conforming to required specifications
Small holes or cuts in fuel vapor hoses/tubes
Canister vent solenoid stays partially open on closed command
Damaged, cross-threaded or loosely installed fuel filler cap
Loose fuel vapor hose/tube connections to EVAP system components
EVAP system component seals leaking (EVAP canister purge valve, fuel tank pressure sensor, canister vent solenoid, fuel vapor control valve tube
assembly or fuel
vapor vent valve assembly)
P0443 – EVAP Control System Canister Purge Valve Circuit Malfunction The PCM monitors the EVAP canister purge valve circuit for an electrical failure.
The
test fails when the signal moves outside the minimum or maximum allowable calibrated parameters for a specified purge duty cycle by PCM command.
VPWR
circuit open
EVAP canister purge valve circuit shorted to GND
Damaged EVAP canister purge valve
EVAP canister purge valve circuit open
EVAP canister purge valve circuit shorted to VPWR
Damaged PCM
Monitor EVAPPDC PID and voltage between EVAP canister valve signal and PWR GND in output test mode with key ON engine OFF (or in key ON engine
RUNNING mode). EVAPPDC PID at 0% and voltage less than 1.0 volts (or EVAPPDC PID at 100% and voltage less than 0.5 volts) indicates a hard fault.
P0451 – FTP Sensor Circuit Noisy The fuel tank pressure changes greater than 14 inches of H 2 0 in 0.10 seconds. Intermittent open or short in the FTP
sensor or
the FTP sensor signal.
Monitor FTP PID and does it change from above 15 inches of H 2 0 to below a minus (-) 15 inches of H 2 0 often in 1.0 minute.
P0452 – FTP Sensor Circuit Low Voltage Detected The PCM monitors the EVAP control system FTP sensor input signal to the PCM. The test fails when the
signal average drops below a minimum allowable calibrated parameter. Contamination internal to FTP sensor connector
Damaged PCM
FTP circuit shorted to GND or SIG RTN
Damaged FTP sensor
FTP V PID reading less than 0.22 volt with key ON and engine OFF or during any engine operating mode indicates a hard fault.
P0453 – FTP Sensor Circuit High Voltage Detected The PCM monitors the EVAP control system FTP sensor input signal to the PCM. The test fails when
the
signal average jumps above a minimum allowable calibrated parameter. FTP circuit open
VREF shorted to VPWR
Damaged PCM
FTP circuit shorted to VREF or VPWR
SIG RTN circuit open
Damaged FTP sensor
FTP V PID reading greater than 4.50 volts with key ON and engine OFF or during any engine operating mode indicates a hard fault.
P0455 – EVAP Control System Leak Detected (No Purge Flow or Large Leak) The PCM monitors the complete EVAP control system for no purge flow, the
presence of a large fuel vapor leak or multiple small fuel vapor leaks. The system failure occurs when no purge flow (attributed to fuel vapor blockages or
restrictions), a large fuel vapor leak or multiple fuel vapor leaks are detected by the EVAP running loss monitor test with the engine running (but not at
idle).
After-market EVAP hardware (such as fuel filler cap) non-conforming to required specifications
Disconnected or cracked fuel EVAP canister tube, EVAP canister purge outlet tube or EVAP return tube
EVAP canister purge valve stuck closed
Damaged EVAP canister
Damaged or missing fuel filler cap
Insufficient fuel filler cap installation
Loose fuel vapor hose/tube connections to EVAP system components
Blockages or restrictions in fuel vapor hoses/tubes (items also listed under disconnections or cracks)
Fuel vapor control valve tube assembly or fuel vapor vent valve assembly blocked
Canister vent (CV) solenoid stuck open
Mechanically inoperative fuel tank pressure (FTP) sensor
Check for audible vacuum noise or significant fuel odor in the engine compartment or near the EVAP canister and fuel tank.
P0456 – EVAP Control System Leak Detected (Very Small Leak) The PCM monitors the complete EVAP control system for the presence of a very small fuel
vapor leak. The system failure occurs when a fuel vapor leak from an opening as small as 0.508 mm (0.020 inch) is detected by the EVAP running loss
monitor test.
Very small holes or cuts in fuel vapor hoses/tubes.
Loose fuel vapor hose/tube connections to EVAP system components.
EVAP system component seals leaking (refer to Possible Causes under DTC P0442).
P0457 – EVAP Control System Leak Detected (Fuel Filler Cap Loose/Off) A fuel tank pressure change greater than a minus (-) 7 inches of H 2 0 in 30
seconds
has occurred after refueling; or there is excessive purge (fuel vapor) flow greater than 0.06 pounds per minute. Fuel filler cap not installed on refueling
(storing
continuous memory DTC) and “check Fuel Cap” light may also be illuminated.
Fuel filler cap missing, loose or cross-threaded.
Check for missing fuel filler cap or integrity of the cap. If OK, clear continuous memory DTCs and re-initiate EVAP Emission Running Loss Monitor Drive
Cycle.
P0460 – Fuel Level Sensor Circuit Malfunction The PCM monitors the fuel level input (FLI) circuit for electrical failure. The test fails when the signal moves
outside
the minimum or maximum allowable calibrated parameters for a specified fuel fill percentage in the fuel tank. Empty fuel tank
Fuel pump (FP) module stuck open
Incorrectly installed fuel gauge
Damaged instrument cluster
CASE GND circuit open
FLI shorted to VPWR
Damaged PCM
Overfilled fuel tank
Fuel pump (FP) module stuck closed
Damaged fuel gauge
FLI circuit open
FLI circuit shorted to CASE GND or PWR GND
CSE GND shorted to VPWR
Monitor FLI PID and FLI V PID in key ON engine RUNNING. FLI PID at 25% fill (with non matching fuel gauge) and FLI V PID less than 0.90 volts [for FLI
PID at 75% fill (with non matching fuel gauge) and FLI V PID greater than 2.45 volts] indicates a hard fault.
P0500 – Vehicle Speed Sensor (VSS) Malfunction Indicates the powertrain control module (PCM) detected an error in the vehicle speed information.
Vehicle
speed data is received from either the vehicle speed sensor (VSS), transfer case speed sensor (TCSS), anti-lock brake system (ABS) control module,
generic
electronic module (GEM), or central timer module (CTM). If the engine rpm is above the torque converter stall speed (automatic transmission) and engine
load is
high, it can be inferred that the vehicle must be moving. If there is insufficient vehicle speed data input, a malfunction is indicated and a DTC is set. On
most vehicle
applications the malfunction indicator lamp (MIL) will be triggered when this DTC is set. Open in VSS+/VSS- harness circuit.
Open in TCSS signal or TCSS signal return harness circuit.
Short to GND in VSS harness circuit.
Short to GND in TCSS harness circuit.
Short to PWR in VSS harness circuit.
Short to PWR in TCSS harness circuit.
Open or short in the vehicle speed circuit(s) (VSC) between the PCM and appropriate control module.
Damaged VSS or TCSS.
Damaged wheel speed sensors.
Damaged wheel speed sensor harness circuits.
Damage in module(s) connected to VSC/VSS circuit.
Damage drive mechanism for VSS or TCSS.
Monitor VSS PID while driving vehicle. This DTC is set when the PCM detects a sudden loss of vehicle speed signal over a period of time. If vehicle speed
data is
lost, check the source of where the vehicle speed input originates from: VSS, TCSS, ABS, GEM or CTM. Note: On some MSOF applications, VSS and
TCSS
PID can be monitor. However if no TCSS PID is available and VSS PID is zero, TCSS circuitry frequency must be checked for loss of sensor signal. If
another
vehicle electronic module has generated the P0500 and the vehicle does not receive its vehicle speed input from one of the above mention sources (VSS,
TCSS,
ABS, GEM or CTM). Check the PCM for Output Shaft Speed Sensor (OSS) DTCs. On OSS applications the PCM uses the OSS to calculated the vehicle
speed. If no OSS DTCs are found check for correct PCM configuration. Check PCM configuration for correct tire size and axle ratio.
P0501 – Vehicle Speed Sensor (VSS) Range/ Performance Indicates the powertrain control module (PCM) detected an error in the vehicle speed
information. This
DTC is set the same way as P0500, however the malfunction indicator lamp (MIL) is not triggered. Refer to possible causes for P0500.
Refer to diagnostic aids for P0500.
P0503 – Vehicle Speed Sensor (VSS) Intermittent Indicates poor or noisy VSS performance. Vehicle speed data is received from either the vehicle speed
sensor
(VSS), transfer case speed sensor (TCSS), anti-lock brake system (ABS) control module, generic electronic module (GEM), or central timer module (CTM).
Noisy VSS/TCSS input signal from Radio Frequency Interference/ Electro-Magnetic Interference (RFI/EMI) external sources such as ignition components or
charging circuit.
Damaged VSS or driven gears.
Damaged TCSS.
Damaged wiring harness or connectors.
Malfunction in module(s) or circuit connected to VSS/TCSS circuit.
After market add-on.
Monitor VSS PID while driving vehicle, check for intermittent vehicle speed indication. Verify ignition and charging system are functioning correctly.
P0505 – Idle Air Control System Malfunction The PCM attempts to control engine speed during KOER self-test. The test fails when the desired rpm could
not be
reached or controlled during the self-test. IAC circuit open
VPWR to IAC solenoid open
IAC circuit shorted to PWR
Air inlet is plugged
Damaged IAC valve
Damaged PCM
The IAC solenoid resistance is from 6 to 13 ohms.
P0552 – Power Steering Pressure (PSP) Sensor Circuit Malfunction The PSP sensor input signal to the PCM is continuously monitored.The test fails when
the
signal is open or shorted to ground. PSP sensor damaged
SIG RTN circuit open or shorted
VREF circuit open or shorted
PSP sensor signal circuit open or shorted
Damaged PCM
The DTC indicates the PSP sensor circuit is open or shorted to ground.
P0553 – Power Steering Pressure (PSP) Sensor Circuit Malfunction The PSP sensor input signal to PCM is continuously monitored. The test fails when the
signal is
shorted to power. PSP sensor damaged
SIG RTN circuit shorted to power
VREF circuit shorted to power
PSP sensor signal circuit shorted to power
Damaged PCM
The code indicates the PSP sensor circuit is shorted to power.
P0602 – Control Module Programming Error This Diagnostic Trouble Code (DTC) indicates programming error within Vehicle ID block (VID). VID data
corrupted by the scan tool during VID reprogramming
Using the scan tool, reprogram the VID block. If PCM does not allow reprogramming of the VID block, reflashing PCM will be required.
P0603 – Powertrain Control Module KAM Test Error Indicates the PCM has experienced an internal memory fault. However there are external items that can
cause this DTC. Reprogramming
Battery terminal corrosion
KAPWR to PCM interrupt/open
Loose battery connection
Damaged PCM
If KAPWR is interrupted to the PCM because of a battery or PCM disconnect, DTC can be generated on the first power-up.
P0605 – PCM read only memory (ROM) error Indicates the PCM ROM has been corupted. An attempt was made to change the calibration.
Module programming error.
Damaged PCM
Reprogram or update calibration.
Reprogram VID block (use as built data).
Check for other DTC’s or drive symptoms for further action.
P0703 – Brake Switch Circuit Input Malfunction Indicates PCM did not receive a brake pedal position (BPP) input. Open or short in BPP circuit
Open or short in stoplamp circuits
Damaged PCM
Malfunction in module(s) connected to BPP circuit. (Rear Electronic Module [REM] Windstar and LS6/LS8 or Lighting Control Module (LCM) Continental
and
Town Car.
Damaged brake switch
Misadjusted brake switch
Check for proper function of stoplamps. Follow correct Self-Test procedures, refer to Section 2 of Quick Test.
P0704 – Clutch Pedal Position Switch Malfunction When the clutch pedal is depressed the voltage goes to low. If the PCM does not see this change from
high to
low the DTC is set. CPP circuit short to PWR
Damaged CPP switch
CPP circuit open in the SIGRTN
Damaged PCM
When depressing the CPP switch the voltage should cycle from 5.0V down.
P0720 – Insufficient input from Output Shaft Speed sensor The output shaft speed sensor inputs a signal to the PCM, based on the speed of the output
shaft of the
transmission. The PCM compares this signal with the signal of the VSS or TCSS and determines correct tire size and axle gear ratio. OSS sensor circuit
short to
GND
OSS sensor circuit short to PWR
OSS sensor circuit open
Damaged OSS sensor
Damaged PCM
Verify sensor signal output varies with vehicle speed.
P0721 – Noise interference on Output Shaft Speed sensor signal The output shaft speed sensor signal is very sensitive to noise. This noise distorts the
input to the
PCM. Wiring misrouted
After market add-on
Wiring damaged
Wiring insulation wear
Check routing of harness.
Check wiring and connector for damage.
P0722 – No signal from Output Shaft Speed sensor The output shaft speed sensor failed to provide a signal to the PCM upon initial movement of vehicle.
Damaged
OSS connector
Damaged OSS sensor, or not installed properly
Harness intermittently shorted or open
P0723 – Output Shaft Speed sensor circuit intermittent failure The output shaft speed sensor signal to the PCM is irregular or interrupted. Harness
connector not
properly seated
Harness intermittently shorted, or open
Harness connector damaged
OSS sensor damaged, or not installed properly
Verify harness and connector integrity
Verify OSS sensor proper installation
P0812 – Reverse Switch (RS) input circuit malfunction The DTC indicates that the voltage is high when it should be low. Transmission shift not indicating
neutral
while in KOEO Self-Test
RS circuit short to PWR
Damaged reverse switch
RS circuit open or short to SIGRTN
Damaged PCM
Check RS PID while exercising shift lever in and out of reverse.
P1000 – Monitor Testing Not Complete The on board diagnostic II (OBD II) monitors are performed during the OBD II Drive Cycle. The DTC will be stored in
continuous memory if any of the OBD II monitors do not complete. Vehicle is new from the factory
Battery or PCM had recently been disconnected
An OBD II monitor failure had occurred before completion of an OBD II drive cycle
PCM DTCs have recently been cleared with a scan tool
PTO circuit is shorted to VPWR or B+ or PTO is on during testing
The DTC does not need to be cleared from the PCM except to pass an inspection/maintenance test.
P1001 – KOER Not Able To Complete, KOER Aborted This Non-MIL (Malfunction Indicator Lamp) code will be set when Key On Engine Running (KOER)
Self-Test does not complete in the time intended. Incorrect Self-Test Procedure.
Unexpected response from Self-Test monitors.
rpm out of specification.
Rerun Self-Test following QT1 in Section 3 , Symptom Charts, STEP 1: PCM Quick Test.
P1100 – Mass Air Flow (MAF) Sensor Intermittent The MAF sensor circuit is monitored by the PCM for sudden voltage (or air flow) input change through
the
comprehensive component monitor (CCM). If during the last 40 warm-up cycles in key ON engine running the PCM detects a voltage (or air flow) change
beyond
the minimum or maximum calibrated limit, a continuous memory diagnostic trouble code (DTC) is stored. Poor continuity through the MAF sensor
connectors
Poor continuity through the MAF sensor harness
Intermittent open or short inside the MAF sensor.
While accessing the MAF V PID on the scan tool, lightly tap on the MAF sensor or wiggle the MAF sensor connector and harness. If the MAF V PID
suddenly
changes below 0.23 volt or above 4.60 volts, an intermittent fault is indicated.
P1101 – Mass Air Flow (MAF) Sensor Out of Self-Test Range The MAF sensor circuit is monitored by the PCM for an out of range air flow (or voltage)
input. If
during key ON engine OFF the air flow voltage signal is greater than 0.27 volts the test fails. Likewise, if during key ON engine running, an air flow voltage
signal is
not within 0.46 volt to 2.44 volts, the test fails. For voltage to air flow gm/sec conversion, GO to Pinpoint Test DC and refer to Voltage To Mass Air Flow
Conversion Table. Low battery charge
MAF sensor partially connected
MAF sensor contamination
PWR GND open to MAF sensor
MAF RTN circuit open to PCM
Damaged MAF sensor
Damaged PCM
A MAF V PID reading greater than 0.27 volts (KOEO) or a MAF V PID reading outside the 0.46 volt to 2.44 volts range (KOER) indicates a hard fault.
P1112 – Intake Air Temperature (IAT) Sensor Intermittent Indicates IAT sensor signal was intermittent during the comprehensive component monitor.
Damaged
harness
Damaged sensor
Damaged harness connector
Damaged PCM
Monitor IAT on scan tool, look for sudden changes in reading when harness is wiggled or sensor is tapped.
P1114 – Intake Air Temperature 2 Circuit Low Input Indicates the sensor signal is less than Self-Test minimum. The IAT2 sensor minimum is 0.2 volts.
Grounded
circuit in harness
Improper harness connection
Damaged sensor
Damaged PCM
Monitor IAT2 PID. Typical IAT2 temperature should be greater than IAT1. Refer to Section 6 : Reference Values for ranges.
P1115 – Intake Air Temperature 2 Circuit High Input Indicates the sensor signal is greater than Self-Test maximum. The IAT2 sensor maximum is 4.6 volts.
Open
circuit in harness
Sensor signal short to power
Improper harness connection
Damaged sensor
Damaged PCM
Monitor IAT2 PID. Typical IAT2 temperature should be greater than IAT1. Refer to Section 6 : Reference Values for ranges.
P1116 – Engine Coolant Temperature (ECT) Sensor Out of Self-Test Range Indicates the ECT sensor is out of Self-Test range. Correct range is 0.3 to
3.7 volts.
Overheating condition
Malfunctioning thermostat
Damaged ECT sensor
Low engine coolant
Damaged harness connector
Damaged PCM
Engine coolant temperature must be greater than 10°C (50°F) to pass the KOEO Self-Test and greater than 82°C (180°F) to pass the KOER Self-Test.
P1117 – Engine Coolant Temperature (ECT) Sensor Intermittent Indicates ECT circuit became intermittently open or shorted while engine was running.
Damaged
harness
Damaged sensor
Damaged PCM
Damaged harness connector
Low engine coolant
Monitor ECT on scan tool, look for sudden changes in reading when harness is wiggled or sensor is tapped.
P1120 – Throttle Position (TP) Sensor Out of Range Low (RATCH too Low) The TP sensor circuit is monitored by the PCM for a low TP rotation angle (or
voltage) input below the closed throttle position through the comprehensive component monitor (CCM). If during key ON engine OFF or key ON engine
running
the TP rotation angle (or voltage) remains within the calibrated self-test range but falls between 3.42 and 9.85% (0.17 and 0.49 volt), the test fails. TP
circuit with
frayed wires
Corrosion on TP circuit connectors
VREF open to TP sensor
VREF short to SIG RTN
TP sensor loose pins
A TP PID (TP V PID) between 3.42 and 9.85% (0.17 and 0.49 volt) in key ON engine OFF, continuous memory or key ON engine running indicates a hard
fault.
P1121 – Throttle Position (TP) Sensor Inconsistent with MAF Sensor The PCM monitors a vehicle operation rationality check by comparing sensed throttle
position to mass air flow readings. If during key ON engine running self-test the comparison of the TP sensor and MAF sensor readings are not consistent
with
calibrated load values, the test fails and a diagnostic trouble code is stored in continuous memory. Air leak between MAF sensor and throttle body
TP sensor not seated properly
Damaged TP sensor
Damaged MAF sensor
Drive vehicle and exercise throttle and TP sensor in all gears. A TP PID (TP V PID) less than 4.82 % (0.24 volt) with a LOAD PID greater than 55% or a TP
V
PID greater than 49.05% (2.44 volts) with a LOAD PID less than 30% indicates a hard fault.
P1124 – Throttle Position (TP) Sensor Out of Self-Test Range The TP sensor circuit is monitored by the PCM for an out of range TP rotation angle (or
voltage)
input. If during key ON engine OFF or key ON engine running the TP rotation angle (or voltage) reading is less than 13.27% (0.66 volt) or greater than
23.52%
(1.17 volts), the test fails. Binding or bent throttle linkage
TP sensor not seated properly
Throttle plate below closed throttle position
Throttle plate/screw misadjusted
Damaged TP sensor
Damaged PCM
A TP PID (TP V PID) reading not between 13.27 and 23.52% (0.66 and 1.17 volts) in key ON engine OFF or key ON engine running indicates a hard fault.
P1125 – Throttle Position (TP) Sensor Intermittent The TP sensor circuit is monitored by the PCM for sudden TP rotation angle (or voltage) input change
through
the comprehensive component monitor (CCM). If during the last 80 warm-up cycles in key ON engine running the PCM detects a TP rotation angle (or
voltage)
changes beyond the minimum or maximum calibrated limit, a continuous diagnostic trouble code (DTC) is stored. Poor continuity through the TP sensor
connectors
Poor continuity through the TP harness
Intermittent open or short inside the TP sensor
While accessing the TP V PID on the scan tool, lightly tap on the TP sensor or wiggle the TP sensor connector and harness. If the TP V PID suddenly
changes
below 0.49 volt or above 4.65 volts, an intermittent fault is indicated.
P1127 – Exhaust Not Warm Enough, Downstream Sensor Not Tested The HEGO monitor uses an exhaust temperature model to determine when the HO2S
heaters are cycled ON. The test fails when the inferred exhaust temperature is below a minimum calibrated value. Engine not operating long enough prior
to
performing KOER self-test.
Exhaust system too cool.
Monitor HO2S Heater PIDs to determine their ON/OFF state. DTC P1127 will be present if the exhaust is not hot.
P1128 – Upstream Oxygen Sensors Swapped from Bank to Bank (HO2S-11-21) The HEGO monitor checks and determines if the HO2S signal response
for a
fuel shift corresponds to the correct engine bank. The test fails when a response from the HO2S(s) being tested is not indicated. Crossed HO2S harness
connectors
(upstream).
Crossed HO2S wiring at the harness connectors (upstream).
Crossed HO2S wiring at the 104-pin harness connectors (upstream).
P1129 – Downstream Oxygen Sensors Swapped from Bank to Bank (HO2S-12-22) The HEGO monitor checks and determines if the HO2S signal response
for a
fuel shift corresponds to the correct engine bank. The test fails when a response from the HO2S(s) being tested is not indicated. Crossed HO2S harness
connectors
(downstream).
Crossed HO2S wiring at the harness connectors (downstream).
Crossed HO2S wiring at the 104-pin harness connectors (downstream).
P1130 – Lack of HO2S-11 Switch, Fuel Trim at Limit The HEGO Sensor is monitored for switching. The test fails when the HO2S fails to switch due to
circuit or
fuel at or exceeding a calibrated limit. Electrical:
Short to VPWR in harness or HO2S
Water in harness connector
Open/Shorted HO2S circuit
Corrosion or poor mating terminals and wiring
Damaged HO2S
Damaged PCM
Fuel System:
Excessive fuel pressure
Leaking/contaminated fuel injectors
Leaking fuel pressure regulator
Low fuel pressure or running out of fuel
Vapor recovery system
Induction System:
Air leaks after the MAF
Vacuum Leaks
PCV system
Improperly seated engine oil dipstick
EGR System:
Leaking gasket
Stuck EGR valve
Leaking diaphragm or EVR
Base Engine:
Oil overfill
Cam timing
Cylinder compression
Exhaust leaks before or near the HO2S(s)
A fuel control HO2S PID switching across 0.45 volt from 0.2 to 0.9 volt indicates a normal switching HO2S.
P1131 – Lack of HO2S-11 Switch, Sensor Indicates Lean A HEGO sensor indicating lean at the end of a test is trying to correct for an over-rich condition.
The
test fails when the fuel control system no longer detects switching for a calibrated amount of time. See Possible Causes for DTC P1130
P1132 – Lack of HO2S-11 Switch, Sensor Indicates Rich A HEGO sensor indicating rich at the end of a test is trying to correct for an over-lean condition.
The
test fails when the fuel control system no longer detects switching for a calibrated amount of time. See Possible Causes for DTC P1130
P1137 – Lack of HO2S-12 Switch, Sensor Indicates Lean The downstream HO2S sensors are forced rich and lean and monitored by the PCM. The test
fails if
the PCM does not detect the output of the HO2S in a calibrated amount of time. Pinched, shorted, and corroded wiring and pins
Crossed sensor wires
Exhaust leaks
Contaminated or damaged sensor
P1138 – Lack of HO2S-12 Switch, Sensor Indicates Rich See DTC P1137
P1150 – Lack of HO2S-21 Switch, Fuel Trim at Limit See DTC P1130
P1151 – Lack of HO2S-21 Switch, Sensor Indicates Lean A HEGO sensor indicating lean at the end of a test is trying to correct for an over-rich condition.
The
test fails when fuel control system no longer detects switching for a calibrated amount of time. See Possible Causes for DTC P1130
P1152 – Lack of HO2S-21 Switch, Sensor Indicates Rich A HEGO sensor indicating rich at the end of a test is trying to correct for an over-lean condition.
The
test fails when the fuel control system no longer detects switching for a calibrated amount of time. See Possible Causes for DTC P1130
P1157 – Lack of HO2S-22 Switch, Sensor Indicates Lean See DTC P1137
P1158 – Lack of HO2S-22 Switch, Sensor Indicates Rich See DTC P1137
P1168 – Fuel Rail Pressure Sensor in Range But Low The comprehensive component monitor (CCM) monitors the FRP pressure for acceptable fuel
pressure. The
test fails when the fuel pressure falls below a calibrated value. Low fuel pressure
Damaged FRP sensor
Excessive resistance in circuit
Low or no fuel
A FRP PID value below 551 kpa (80 psi) indicates a failure
Low or no fuel
A FRP PID value greater than 896 kpa (130 psi) indicates a failure